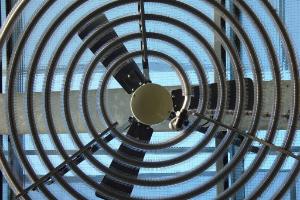
By Camilo Botero*
Very often we are faced with projects of a certain size that must be properly managed and more so today where we must ensure that they are sustainable over time, energy saving and friendly to the environment.
We always resort to a Project Management, to a Technical Audit, we rarely use the concept of Technological Management and little or nothing the "Commissioning" (it does not have a translation that has the meaning you want in Spanish, so and with the reader's license, I will use that term in this article, it could also be used "Assurance", but it is not yet known).
ASHRAE, in its Guideline 0-2005 in its prologue defines it as: "A quality-oriented process to achieve, verify and document that the performance of facilities, systems and assemblies meet the objectives and criteria previously defined".
Continuing the definition, in ASHRAE's 1.1 guide: "HVC&R Technical Requirements for the Commissioning Process" of 2007, he adds: "The Commissioning group uses a variety of methods and tools so that the project is meeting the Owner's Project Requirements (OPR)."
This concept of Commissioning has been used by the United States Navy since the middle of the last century and they defined it as "Placing a vessel in service". ASHRAE formally began in 1982 when a committee was constituted to document the best practices for the facilities to meet the requirements of the project owner, hence the "commissioning guidelines" that have been evolving to those mentioned above.
During the Annual Meeting 2010 in Albulquerque, NM, United States, I had the opportunity to take a course on the subject taught by Walter T. Grondzik PE, who has a book on the subject and which I will take advantage of to try to give an overview of the quality assurance process, in Air Conditioning projects, Cooling and Ventilation.
In this course Professor Grondzik wrote: What is The Commissioning (Cx) of Buildings? It is a quality-focused process to improve the delivery of a project. The process focuses on verification and documentation so that the installation and all systems are planned, designed, installed, tested, operated and maintained to meet the requirements of the owner and limits saying that Commissioning is a structured quality assurance process that aims to ensure that the building, when delivered, meet the requirements of the project and that it is NOT an event, NOR a short-term task, NOR the verification of a checklist.
All of the above seems too obvious and / or simple, but there are statistics that confirm that three months after having started a system of those in question, it has lost 30% or more of its design conditions, if it has not been operated and maintained properly, with its negative consequences in compliance with the design parameters (for example lack of comfort), in a greater consumption of energy, which in turn brings a greater impact on the environment.
There are four very defined phases in any project that must have a quality assurance process:
*Pre-design
*Design
*Construction
*Occupation and Operation.
We are all experts in our professions, we are well trained to design, build, operate and maintain our buildings efficiently and effectively, so why so much inefficiency, failures, non-compliance with specifications, excess pollution? What are we doing wrong?
What happens is that "there is a high fragmentation between the design, construction and operation of the parts of the 'lead team' that leads to duplications, conflicts and inappropriate use of resources," says Commissioning expert, today Bohannan PE.
Each phase of the project and the transition between phases of it, have pitfalls that negatively affect the probability of achieving quality assurance.
Commissioning is essentially a process that facilitates and ensures the following aspects, through the different phases and disciplines involved: Communication, Documentation and Verification, Filling the coordination gaps between civil, mechanical, electrical, hydraulic, data, fire protection engineers; the architects and the different contractors.
The Keys to a successful Commissioning process would be:
1.Clear and precise specifications and correct document archiving.
1.1. Project requirements specified by the owner
1.2. Basis of design
1.3. Commissioning Plan
1.4. Checklists for construction
1.5. Test protocols
1.6. Training plan
1.7. System Manual
1.8. Reports of the Commissioning process
2. Clear and explicit responsibilities
2.1. Clear responsibility of the authority for Commissioning
2.2. Clear and precise responsibilities of design contractors
2.3. Clear and precise responsibilities of construction contractors
2.4. Clear and precise construction specifications of "who" and "when" in the construction phase.
3 . Meetings, reports and records by the Commissioning team
4-Verification by the Commissioning team of all key elements, regarding the requirements and specifications of the owner.
5-Acceptance by the owner, of all key deliverables of the project
The benefits of Commissioning for a project are then:
1. A project that usually reflects the needs and desires of the owner
2. A project that works perfectly well, with the initial and final occupation assumed
3. A project that is well documented
4. Personnel who are well prepared to operate and maintain the systems
5. A project with clear performance goals and objectives.
6. A project that has benefited from the efforts of the different participants.
7. Satisfied owners and occupants
8. Systems that perform as designed.
9. Better building documentation and systems.
10. Reduced energy use and lower operation and maintenance costs.
11. Reduction of service calls a posteriori, to contractors
12. Improved maintainability of equipment and services.
Finally, I want to leave the following reflections regarding Commissioning, because even if all those involved in a project are clear about their own functions, they must adopt this methodology, which will undoubtedly benefit them greatly.
The owner can benefit from the information obtained from the various parties involved who relate the deliverables, with their requirements, wishes and specifications.
The design team can benefit from the issues that relate the design processes to the implementation of the same in the construction phase and verify if their premises and assumptions were met.
Contractors can benefit from issues that relate construction and quality control processes to design documents.
Commissioning authority can benefit from feedback from all aspects of the process. You can identify any system or assembly that does not meet the owner's requirements and quantify the magnitude of such deviations. It also evaluates their operating conditions.
Ideally, it provides a sense of value to the Commissioning process in the project; without accusing, it highlights the problems suppressed, the improved performance, the coordination achieved, the documentation delivered, etc.
As an epilogue to this writing I tell you that during October from 5 to 7 of this year, the III International Congress of Engineering and Thermal Sciences will be held in Bogotá, in which I have the enormous responsibility and satisfaction of dictating a course on Commissioning, to which I invite my dear readers.
* Camilo Botero is the current president of ACAIRE and president of Camilo Botero Ingenieros Consultores Ltda. He has worked as a teacher in several Colombian universities, guilds and currently in ACAIRE in diploma courses of air conditioning projects, energy efficiency in air conditioning and refrigeration, cogeneration and trigeneration, applied psychometrics, thermodynamics, fluid mechanics, heat transfer and turbomachinery.